HP 3D Digital Texture Library
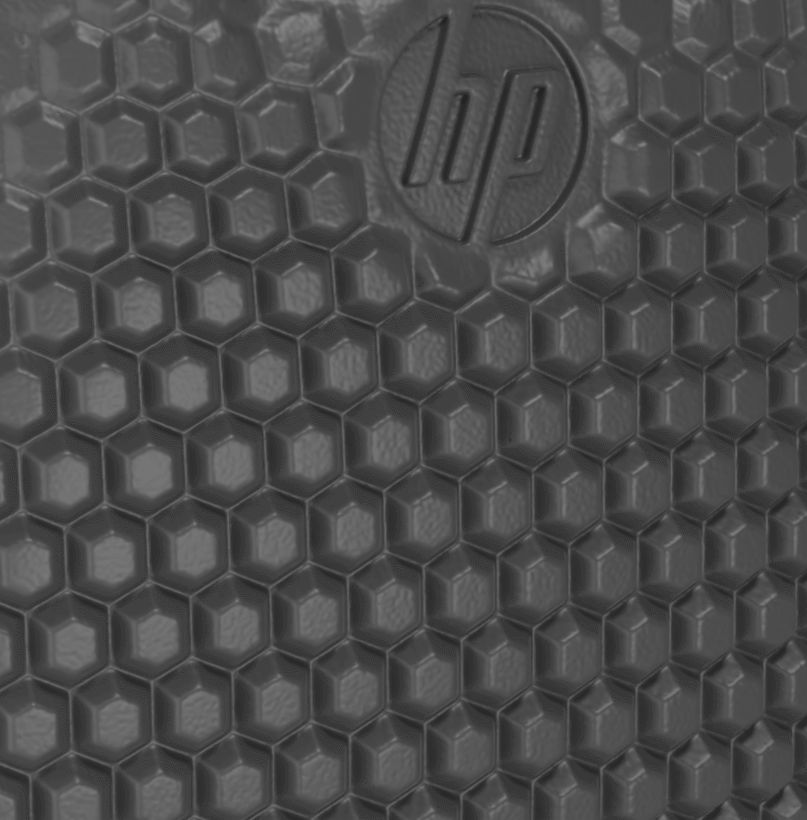
Why 3D Textures?
3D textures on products offer numerous benefits
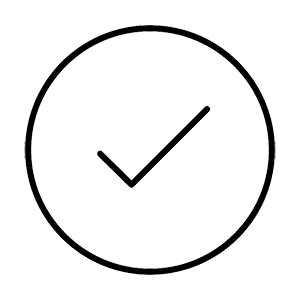
Flawless appearance
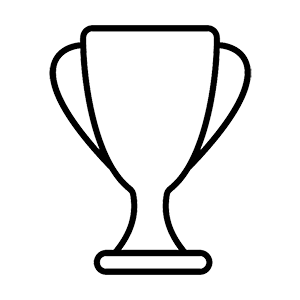
Premium look
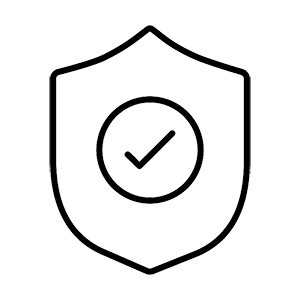
Enhanced durability
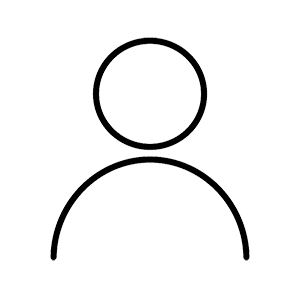
Improved usability
Revolutionize your designs with the HP 3D Digital Texture Library
Featuring over 100 expertly curated digital textures validated for HP's Multi Jet Fusion technology, this innovative tool empowers designers to create stunning, high-quality physical products.
Fill out the form and step into a new era of three-dimensional textures.
You will get access to:
- 3D-printable coupon files
- Digital height maps
- Print recommendations
- Digital catalogue
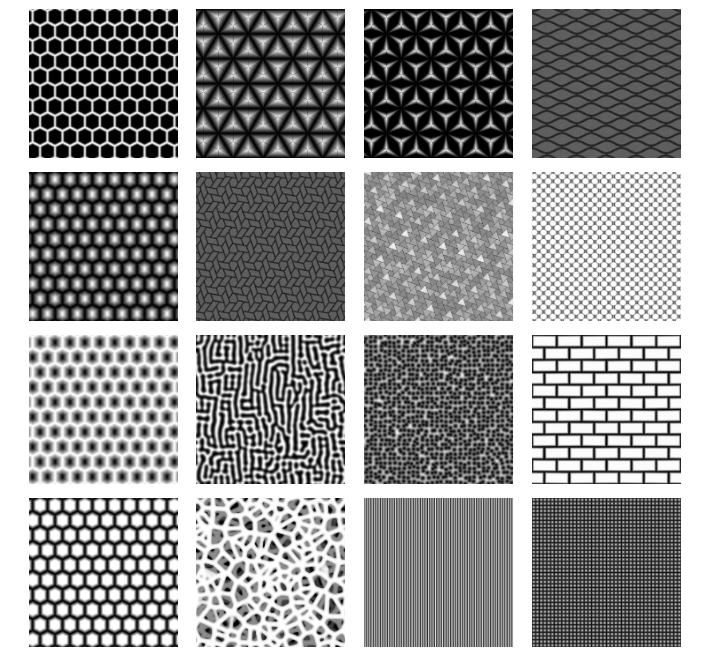
HP 3D Textures Sample Booklet
Would you like to get your hands on a 3D printed sample booklet?
Request it from our HP partner.
HP 3D Texturing Services
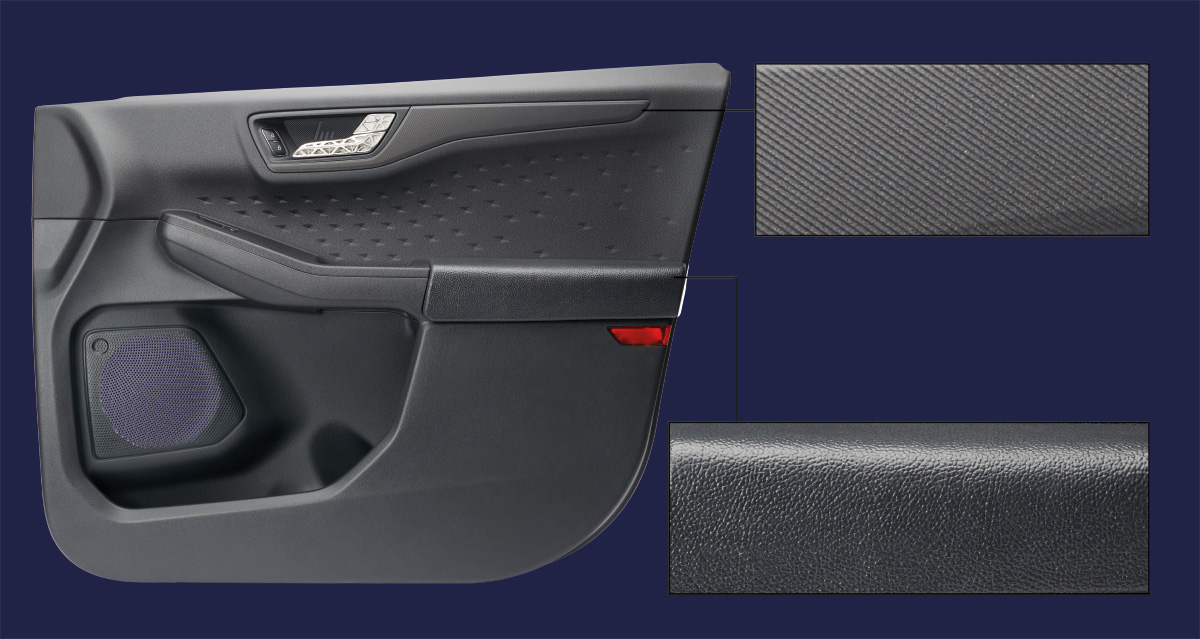
HP’s Digital Texturing Services provide comprehensive support to fully utilize the HP 3D Digital Texture Library.
Whether it’s applying one of HP’s pre-defined textures to your CAD geometry or creating a custom texture from scratch, these services ensure a smooth and efficient integration of digital texturing into your design process
HP 3D Digital Texture Visualization Tool
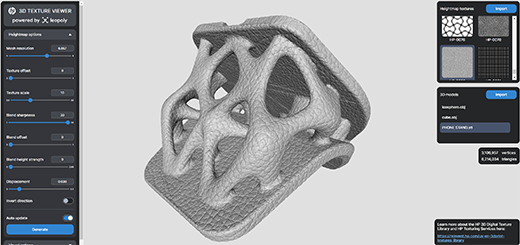
Curious to see an HP texture applied to your geometry in real time? Access the HP 3D Digital Texture Visualization Tool powered by Leopoly.
FAQs
The HP 3D Digital Texture Library was created to fully leverage digital texturing and 3D printing, transforming intricate designs into high-quality physical products. This repository contains over 100 digital texture, with more being added regularly, all validated for use with HP's Multi Jet Fusion technology.
Meticulously curated by HP's CMF (color, material, finish) experts, who also design HP's renowned consumer printers, these texture are based on extensive design trend research to ensure long-term relevance.
Combined with HP’s scalable, production-grade 3D printing, the library offers designers a versatile and innovative tool to break the mold and materialize their design concepts without compromise.
Meticulously curated by HP's CMF (color, material, finish) experts, who also design HP's renowned consumer printers, these texture are based on extensive design trend research to ensure long-term relevance.
Combined with HP’s scalable, production-grade 3D printing, the library offers designers a versatile and innovative tool to break the mold and materialize their design concepts without compromise.
For several decades, adding texture to plastic components has required an expensive, multi-step process centered around injection mold engraving. Traditionally, designers would select a texture from a catalog provided by mold engraving companies. This texture was then applied to mold surfaces through complex laser or chemical etching.
While well-established, this method has significant limitations:
Custom texture are costly and difficult to produce, constrained by the physical and technical limitations of the injection molding process.
These constraints hinder innovation, making it challenging to introduce new texture beyond the standard options that have been used for nearly a generation.
While well-established, this method has significant limitations:
Custom texture are costly and difficult to produce, constrained by the physical and technical limitations of the injection molding process.
These constraints hinder innovation, making it challenging to introduce new texture beyond the standard options that have been used for nearly a generation.
A newer approach to applying texture involves using software to add three-dimensional texture to digital geometries. This method is almost extensively used in the visual effects and video game industries, where high-quality digital assets are essential. It has also become integral to industrial design, allowing designers to create detailed and realistic renderings before moving on to physical prototypes and production.
This digital technique offers unparalleled flexibility, enabling the creation and manipulation of an infinite range of novel texture. However, until now, it has primarily been used for assets intended to remain digital rather than those manufactured as physical products.
This digital technique offers unparalleled flexibility, enabling the creation and manipulation of an infinite range of novel texture. However, until now, it has primarily been used for assets intended to remain digital rather than those manufactured as physical products.